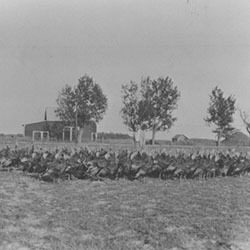
Virgil Cooper begins raising turkeys with his mother. At this time they were raising about 300 turkeys, mainly for the holidays.
Virgil Cooper married Virginia Rockey
Virgil and Virginia moved to Oakwood, Ohio
During this time of World War II, there was a government incentive to produce meat. Virgil had grown his flock to 10,000 turkeys per year during this period
Virgil & Virginia purchased their first hatchery in Oakwood, Ohio. With their increased flock size, no one hatchery was able to supply the Coopers with the number of poults they needed, thus they were having to source with many hatcheries. This hatchery had been one of their suppliers. Purchasing it was a way to be certain they would have the poults they needed
Virgil's brother, Ralph, came from being a manager of a Sears store in Indiana to partner with Virgil. Because Ralph was good at selling appliances, the two deicded to expand the business. Not only was their store in Oakwood a hatchery, but they began also selling appliances, furniture and household goods
After outgrowing the original building in town, the Coopers began construction at the family farm north of Oakwood, on what was to be the first phase of a new hatchery
The Coopers made the first expansion on their turkey hatchery and continued to expand it until 1987, when they built a new hatchery
The Fuller Farm (now known as Apple Creek) was purchased
An 18,000 square foot barn for hens was built at what is now Apple Creek. This location remains in use today as a tom farm and is the origin of the barn and windmill seen in our logo. This was one of the first remote egg producing farms owned by the company
The Adams Farm (now known as Willow Springs) was purchased. Another 18,000 square foot hen barn and a small tom barn were built.
Added more hatchery space in response to the need for more incubator and hatcher capacity
Ralph and Virgil decided that it would be in the family’s best interest to divide the business between the two of them. Ralph took the store and appliance business in town and Virgil took the hatchery and turkey business north of town.
Virgil & Virginia’s eldest son, Jim, leaves his job teaching elementary in California and comes home to join the family business in June.
After attending Bowling Green State University, Gary, the youngest of the three children, moves home and joins the family business in December.
Cooper Hatchery and the Staugler brothers purchased St. Clair Mills. With it, they acquired a feed mill and growout business of 900,000 turkeys per year.
St. Clair Mills and Coopers start in the chicken layer business.
Virgil Cooper decided it was time to retire, leaving the company to his three children.
Dianne, the middle of the three children, joins the family business
September 28, Virgil passed away. He had led his bsuiness through the ups and downs of the industry; since his death, the family has continued to keep that dedication going
Built another hatchery down the street from the other to accommodate all the eggs they would now have from the new breeder farms being built.
In the spring, land was bought in St. Henry, Ohio, where the Harvesting Plant would sit.
In November, construction began on the St. Henry Turkey Harvesting Plant
Began installing automatic egg gathering systems at the breeder hen farms
Bought the Rager plant in Van Wert, Ohio
A dry storage addition was constructed at the St. Henry Turkey Harvesting Plant
Extensive remodeling was done to convert the Van Wert plant into a cooked meats plant. Âé¶¹tv¹ÙÍø brought the building up to spec, put machinery in and gradually added ovens
A new feed mill (known as the North Mill) was constructed in Fort Recovery, Ohio. With additional turkeys needed to supply the Processing Plant, feed manufacturing had to be increased. The 145 foot tall concrete structure was placed two miles north of town and had the capacity to manufacture 450,000 tons of feed per year.
A separate chillder room was added to the St. Henry Turkey Harvesting Plant
Focused Van Wert Plant's business on cooked deli meats
Âé¶¹tv¹ÙÍø began raising commercial market hogs
Âé¶¹tv¹ÙÍø begans selling market hogs
Began automating the poult service line at the Hatchery in Oakwood
Built first sow farm, Rose Grove, in the Oakwood area. This was Âé¶¹tv¹ÙÍø' first attempt at producing their own weaned pigs
St. Henry Harvesting Plant was expanded to add a fabrication room, cooler, loading docks, new offices and a new break room
The stork line deboning was added at the St. Henry Harvesting Plant
An F4 tornado hit Van Wert, Ohio in November and destroys the Cooked Meats Plant
Tore down remains the tornado left of the Van Wert Cooked Meats Plant and completely rebuilt the building. By June the Cooked Meats Plant was running again. The new 72,000 square foot building was designed to have the capacity to cook up to one million pounds per week and had two rooms with state-of-the-art Clean Room Slicing capabilities.
The St. Henry Harvesting Plant enhances capabilities with four value-added cells, a product cooler and more dry storage
The Controlled Atmosphere Stunning was installed at the St. Henry Harvesting Plant
A hog boar stud farm was built in the Antwerp, Ohio area. This farm enabled Âé¶¹tv¹ÙÍø to control the health of their herd in all stages of the process
The St. Henry Harvesting Plant renovates their evisceration room
St. Henry Harvesting Plant removes old chillers and replaces them with new and improved chillders, increasing their capacity to cool
The Van Wert Cooked Meats Plant adds a 30,000 square foot expansion, increasing weekly to 1.3 million pounds
The North Mill in Fort Recovery expands their facility, adding 1,214 more tons of storage for feed processing
The Van Wert Cooked Meats Plant adds a high pressure pasteurizer in the remaining space of the 2010 expansion, providing a high quality pasteurization process for sliced product
Three wind turbiens were installed at the Cooked Meats location to supply clean energy to run the plant. Combined, they provide about 75 percent of the plant's electricity needs
Fox Tail sow farm was built in Defiance County. This is the first farm built with group sow housing and marks the company-wide transition to open-pen gestation
In August, a Biosecurity Building was added in Oakwood. This addition was a key component to maintaining animal health for farms in the Oakwood area
Purchased Fort Recovery Equity, a chicken egg-laying cooperative. The purchase included a feed mill, 75 additional team members and 40 pullet rearing and egg-laying contract farmers
Purchased Perham Ohio jointly with Weaver Eggs. This egg breaking plant, then changed to CW Egg Products, provides the opportunity for value-added liquid egg products
In December, a partnership was announced with Clemens Food Group to build a fresh pork processing plant in Michigan
Sandy Ridge Gilt Farm opens. This farm will raise gilts to maturity and provide the sows for Pheasant Run Sow Farm
In April, Pheasant Run Sow Farm opens in Defiance County. This is the largest sow farm built with group sow housing.
In June, Activate Healthcare, now known as Everside Health, a third party primary care provider, partnered with Âé¶¹tv¹ÙÍø and opened three clinics that are free to all team members who are on Âé¶¹tv¹ÙÍø' insurance
In January, Van Wert Cooked Meats Plant starts to utilize three robots for boxing, stacking and tracking product
In February the completion of a large addition at our St. Henry location was announced. This included a cold storage building and distribution center, new office space, and offal/pet food building.
Acquired Hellegarn & Sons egg production facility, now known as Central Egg Processing
Ashley Biocenter was opened in Ashley, Indiana
Grand Republic, a 5,000-head sow farm, opened in Edgerton, Ohio
Expanded our hogs to 840,000 annually
Acquired full ownership of CW Egg, LLC and rename to Âé¶¹tv¹ÙÍø Liquid Egg Products
Began construction of Golden Heritage Cage-Free Egg Farm
As of September 2022, Golden Heritage houses 1,630,672 layers
Golden Heritage begins full production, holding 2,000,256 birds
Celebrating 85 years as a family-owned and operated company.